Effective warehouse management for small businesses relies on three key elements: smart layout design, inventory control, and streamlined processes. U-shaped, L-shaped, or I-shaped layouts maximize space efficiency, while barcode scanning and automated systems reduce errors. Just-in-Time ordering and ABC analysis help optimize inventory levels, and cross-trained staff increase productivity. Data-driven decisions and performance tracking enable continuous improvement. The path to warehouse excellence begins with these fundamental principles.
Quick Overview
- Choose a suitable layout (U-shaped, L-shaped, or I-shaped) based on your space and order volume to maximize efficiency.
- Implement basic technology solutions like barcode scanning and inventory management software for accurate stock tracking.
- Optimize storage space by utilizing vertical storage and maintaining clear pathways between operational zones.
- Cross-train employees to handle multiple tasks and schedule staff based on order patterns.
- Use data analysis to identify inefficiencies, track performance, and make informed decisions about inventory management.
Smart Layout Design Principles for Small Warehouses
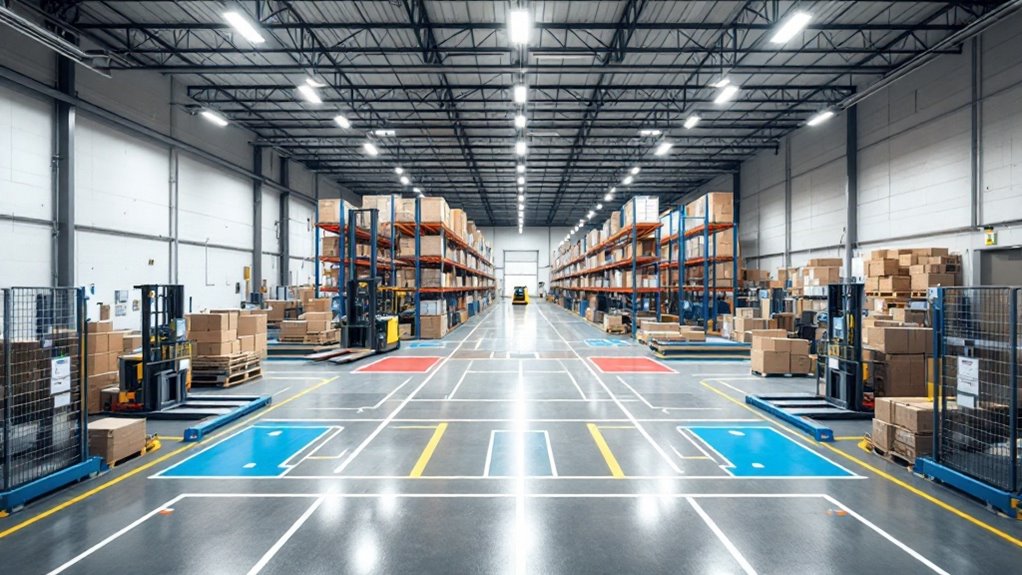
A small warehouse’s success often hinges on its layout design, which serves as the foundation for efficient operations and sustainable growth. Three main layout options provide distinct advantages:
- U-shaped designs offer convenient access to loading areas with centralized storage,
- L-shaped configurations maximize storage along one side,
- and I-shaped layouts create streamlined workflows between receiving and shipping zones.
To optimize these layouts, businesses should focus on strategic placement of key areas. Picking zones work best when positioned near packing and shipping sections, reducing travel time and improving productivity. Clear pathways between different operational zones prevent bottlenecks and enhance workflow efficiency. Implementing directed putaway systems can significantly improve storage optimization and reduce errors. When combined with vertical storage solutions and narrow aisles, these layout principles help small warehouses make the most of limited space while maintaining safe, organized operations.
Essential Inventory Control Systems and Methods
Effective inventory control stands at the heart of successful warehouse management for small businesses. While manual methods using spreadsheets and paper logs remain common, modern solutions offer significant advantages for growing companies.
Small businesses can choose from several proven systems:
- Automated inventory management software provides real-time tracking and integrates with other business systems
- Barcode scanning reduces errors and speeds up stock counts
- Just-in-Time (JIT) ordering minimizes storage costs and improves cash flow
- ABC analysis helps prioritize inventory based on value and importance
The key is selecting a system that matches your business size and needs. Many small warehouses start with basic barcode scanning combined with inventory software, then graduate to more sophisticated solutions as they expand. Regular refresher courses help ensure all team members maintain proficiency with the chosen system. This progressive approach allows for sustainable growth while maintaining accurate stock control.
Choosing the Right Technology Solutions
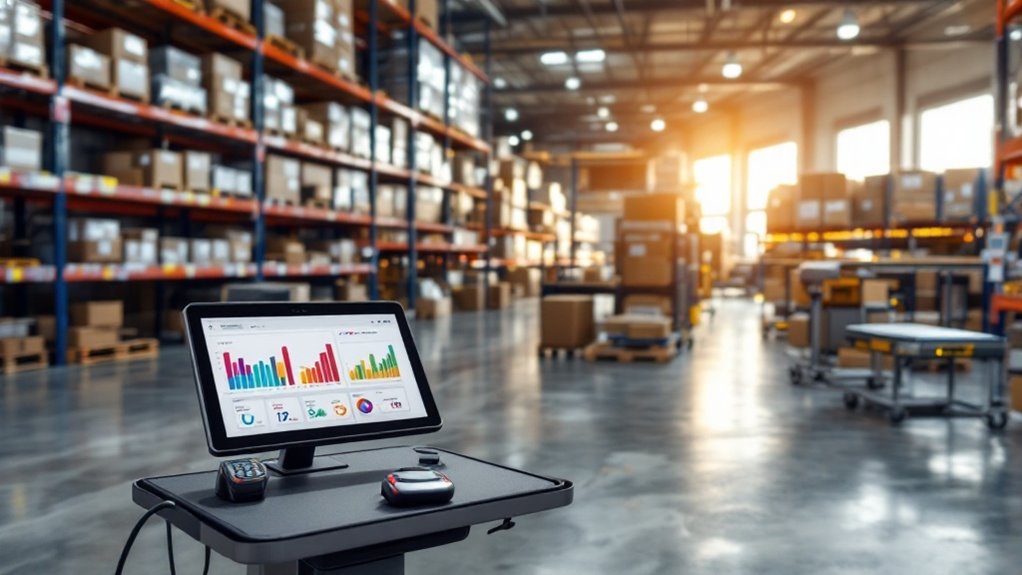
Selecting appropriate technology solutions represents a pivotal decision point for small business warehouse operations. When evaluating options, businesses should focus on systems that offer real-time inventory tracking, order automation, and seamless integration with existing platforms. Lot tracking capabilities enable effective management of product batches and simplified compliance requirements. Modern barcode scanning software can significantly improve inventory accuracy while remaining cost-effective for small businesses.
Technology selection can make or break a small warehouse operation, with real-time tracking and seamless integration driving successful implementations.
Key considerations include:
- Cost-effectiveness through cloud-based solutions and flexible pricing models
- User-friendly interfaces that minimize training requirements
- Integration capabilities with ERP and e-commerce systems
- Scalability to accommodate business growth
Before making a final choice, warehouse managers should:
- Test available demos
- Verify vendor reputation and support services
- Evaluate total implementation costs
- Assess compatibility with current operations
Modern solutions like barcode scanning, RFID technology, and automated picking systems can remarkably improve efficiency while staying within budget constraints. The right technology investment balances immediate needs with future growth potential.
Streamlining Order Processing and Fulfillment
Streamlining order processing and fulfillment is at the heart of successful warehouse operations for small businesses. By implementing efficient systems and automated solutions, businesses can notably reduce errors while enhancing customer satisfaction. Accurate inventory data must be maintained to ensure proper order fulfillment and prevent stockouts.
Process Step | Key Optimization |
---|---|
Order Receipt | Automated OMS allocation |
Picking | Barcode/RFID scanning |
Shipping | Multi-carrier integration |
Small businesses should focus on three core areas to improve their fulfillment operations. First, centralizing order processing through an OMS decreases manual errors and integrates all sales channels. Second, organizing inventory zones and implementing batch picking methods minimizes travel time and boosts efficiency. Finally, partnering with reliable shipping carriers and utilizing automated labeling systems secures timely deliveries while maintaining cost-effectiveness. Regular monitoring of these processes helps identify bottlenecks and opportunities for continuous improvement.
Cost-Effective Operations and Workforce Planning
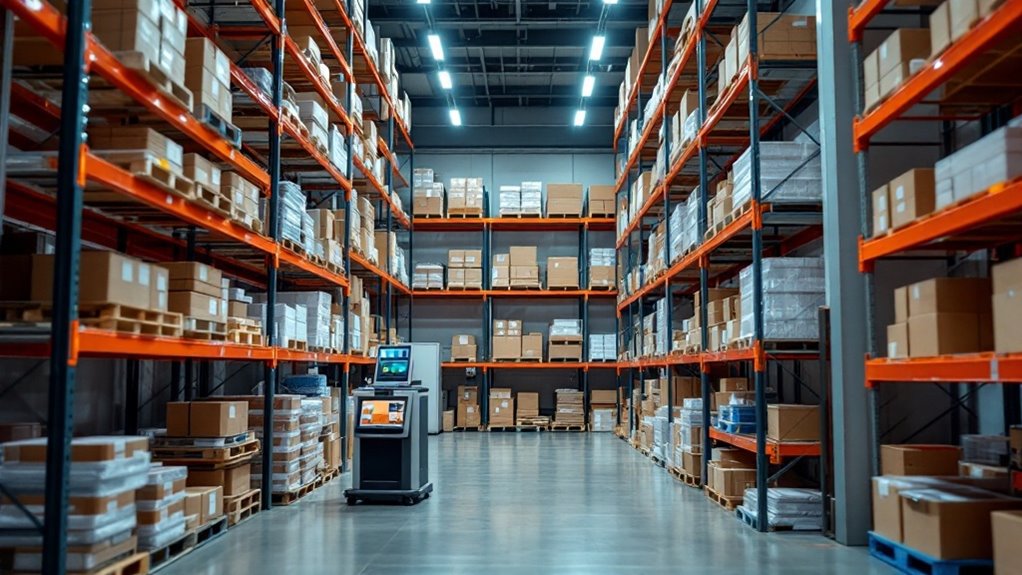
Through careful planning and strategic decision-making, small businesses can markedly reduce warehouse operating costs while maintaining peak productivity. Key strategies include implementing data-driven labor scheduling, cross-training employees, and adopting cost-effective technology solutions.
Small warehouse operators should focus on three main areas:
- Workforce optimization: Schedule staff during peak hours and use seasonal workers during busy periods
- Space utilization: Maximize vertical storage and implement real-time inventory tracking
- Technology integration: Start with basic systems like barcode scanning and gradually adopt more advanced solutions
Regular audits of operational expenses help identify potential savings. Simple changes, such as energy-efficient lighting and standardized packaging materials, can substantially reduce overhead costs. Implementing route optimization software can significantly decrease transportation expenses and improve delivery efficiency. Additionally, cross-training employees creates a flexible workforce that can handle multiple tasks, reducing the need for extra staff during challenging periods.
Using Data Analytics to Drive Growth
Data analytics’ transformative power lies at the heart of modern warehouse management, enabling small businesses to reveal valuable insights from their daily operations. Through centralized data systems, companies can track key performance indicators, monitor inventory levels in real-time, and make data-driven decisions that boost operational efficiency. Modern cloud-based solutions make these capabilities accessible and cost-effective for businesses of all sizes.
By leveraging advanced analytics and machine learning algorithms, small businesses can forecast demand trends, optimize stock levels, and identify seasonal patterns. These insights help prevent stockouts and overstock situations while improving order accuracy. The analysis of customer behavior data allows businesses to tailor their inventory strategies, enhance personalization efforts, and refine marketing campaigns.
Additionally, in-depth data analysis helps identify operational bottlenecks, track revenue growth, and benchmark performance against industry standards, positioning small businesses for sustainable growth and improved competitiveness.
Frequently Asked Questions
How Do I Handle Hazardous Materials Storage in a Small Warehouse?
Proper hazardous materials storage requires dedicated storage cabinets designed for specific material types, with clear labeling and regular inspections. Materials should be segregated based on compatibility, stored in approved containers, and kept in well-ventilated areas with spill containment systems.
Essential safety equipment, including PPE and spill kits, must be readily available. Regular staff training and up-to-date safety documentation are vital. Compliance with OSHA and local regulations is mandatory.
What Insurance Coverage Is Necessary for Warehouse Operations and Stored Inventory?
Essential warehouse insurance coverage includes four key types. Commercial Property Insurance protects the building and fixtures, while Inventory Insurance covers stored goods against theft and damage.
Warehouse Legal Liability Insurance safeguards against claims from third-party goods in storage. Finally, Business Interruption Insurance helps maintain cash flow if operations are disrupted. Together, these policies create an all-inclusive safety net for warehouse operations and stored inventory.
How Can I Prevent Employee Theft in My Warehouse?
To prevent employee theft in warehouses, businesses should implement an extensive security strategy. This includes installing high-definition surveillance cameras, using controlled access systems like key cards or biometric scanners, and maintaining detailed inventory tracking.
Regular security training, background checks for new hires, and establishing an anonymous reporting system are essential. Creating a security-focused culture with clear policies and consequences, while rewarding employee integrity, notably reduces theft risks.
What Government Regulations Apply to Small Warehouse Operations?
Small warehouse operations must comply with several key regulations. OSHA oversees workplace safety requirements, including proper training, emergency plans, and equipment standards.
Employment laws like FLSA govern wages and working hours, while EEOC regulations guarantee fair hiring practices. Proper permits and licenses are needed based on location and stored materials.
Environmental and inventory regulations apply when handling hazardous materials, and fire codes must be followed for safe storage practices.
How Should I Manage Returns and Damaged Goods Processing?
Effective returns management requires a systematic approach. Businesses should establish a dedicated processing area and clear inspection procedures.
Key steps include:
- Sorting returns into categories (resellable, damaged, unsellable)
- Documenting condition and reason for return
- Testing product functionality when applicable
- Determining appropriate disposition (restock, refurbish, liquidate)
- Updating inventory systems promptly
Using barcode scanning and digital tracking helps maintain accuracy. Quick processing minimizes storage costs and preserves product value.
Conclusion
When the rubber meets the road, effective warehouse management can transform a small business’s operations from chaotic to streamlined. By implementing smart layout design, inventory controls, appropriate technology, and data-driven decisions, companies can markedly enhance their efficiency and bottom line. Small warehouse operators who embrace these fundamental principles and continuously refine their processes will be well-positioned to scale operations and maintain competitive advantage in today’s fast-paced market.