Small engine repair software streamlines shop operations through essential features like work order management, inventory control, and customer tracking. Modern solutions offer digital diagnostics, automated scheduling, and financial tools that can reduce labor costs by up to 30% while increasing revenue. Most shops see a return on investment within 6-12 months through improved efficiency and reduced errors. Integration with customer relationship management systems and accounting platforms creates a thorough solution. Understanding the key components helps maximize the software’s transformative potential.
Quick Overview
- Work order management software streamlines repair tracking, scheduling, and technician assignments while reducing manual paperwork and administrative overhead.
- Digital inventory control with barcode scanning ensures accurate parts tracking and automated reordering to prevent stockouts and lost revenue.
- Customer management features store repair histories, automate communications, and provide self-service portals for improved client satisfaction.
- Financial tools automate invoicing, payment processing, and accounting integration, reducing billing errors and improving cash flow.
- Analytics dashboards provide real-time performance metrics and customizable reports to help make data-driven business decisions and track growth.
Essential Features Every Small Engine Repair Software Must Have
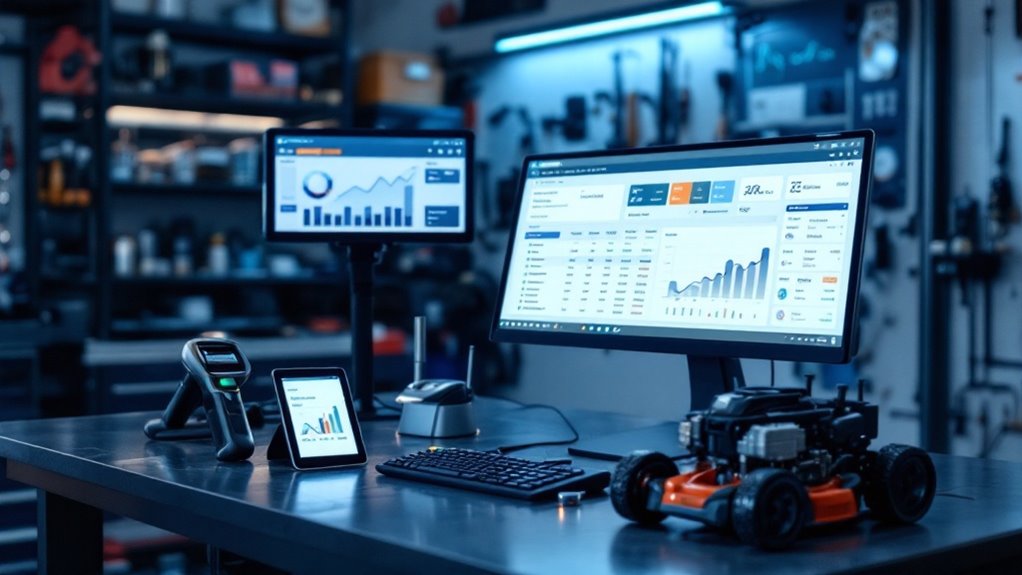
What sets successful small engine repair shops apart from struggling ones? Often, it’s the software they use to streamline their operations. Modern repair shops need extensive software solutions with five core features:
- Work Order Management: Digital tracking of repairs, scheduling, and technician assignments
- Inventory Control: Real-time parts tracking with barcode scanning and automated reordering
- Financial Tools: Automated invoicing, payment processing, and accounting integration
- Customer Management: Centralized database for customer history and automated communications
- Analytics Capabilities: Performance metrics and customizable reporting dashboards
These essential features help shops reduce paperwork, prevent parts shortages, maintain accurate billing, build customer relationships, and make data-driven decisions. Leading software solutions like Contractor+ provide access to 2.5 million supplies through their platform, ensuring repair shops can quickly source needed parts.
When choosing software, guarantee it includes these fundamental capabilities to maximize efficiency and profitability in daily operations.
Selecting the Right Software Solution for Your Repair Shop
While selecting the right software solution represents a crucial decision for any small engine repair shop, owners must carefully evaluate several key factors before making their choice. The software should seamlessly integrate with existing tools, particularly accounting and inventory systems, while offering room for growth as the business expands. Popular solutions like multi-entity management systems can help shops effectively track finances across multiple business locations. Implementing software that supports financial metrics tracking helps owners monitor business performance and make data-driven decisions.
Key considerations include:
Successful software implementation requires analyzing compatibility, vendor support, customization features, scalability options, and system integration capabilities.
- Compatibility with current business processes
- Vendor support and training resources
- Customization options for unique shop needs
- Scalability for future expansion
- Integration capabilities with CRM and booking systems
Shop owners should prioritize solutions that provide thorough onboarding support and ongoing technical assistance. The ideal software package will balance immediate operational needs with long-term growth potential, while offering flexible pricing options that align with the shop’s budget and business goals.
Cost Analysis and Return on Investment
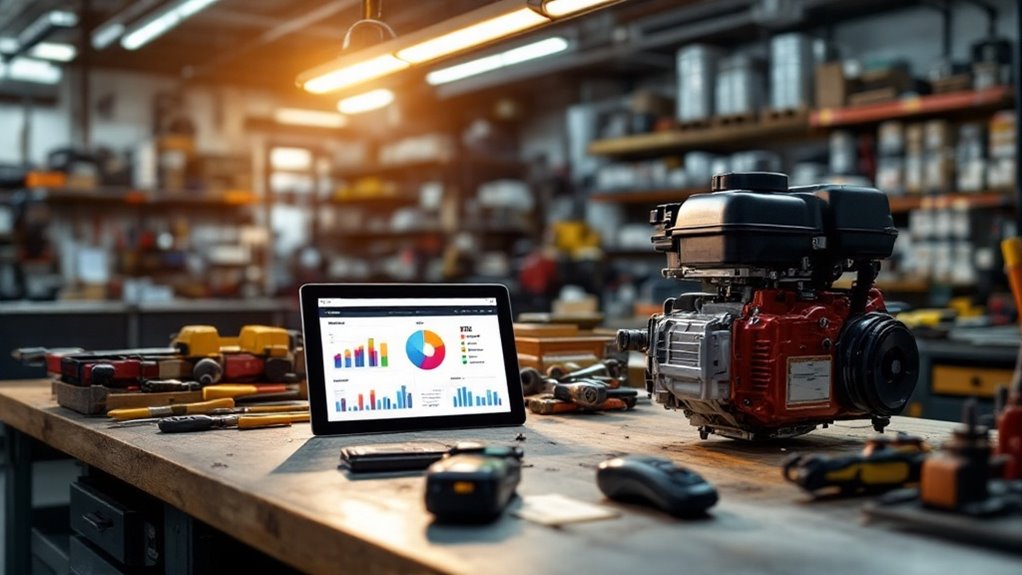
A thorough cost analysis proves essential for small engine repair shops considering software implementation. While initial investments range from $500 to $20,000 depending on the chosen solution, the potential returns considerably outweigh these costs.
Digital inventory management solutions can cut losses and inefficiencies by up to 30% through automated tracking. Upfront expenses include software purchase ($500-$3,000), hardware integration ($1,000-$4,000), and staff training ($500-$2,000).
Operational savings through automation can reduce labor costs by 30%, potentially saving $5,000-$15,000 annually.
Revenue growth opportunities show a 300-500% ROI within the first year, with average payback periods of 6-12 months.
Hidden costs require consideration, including annual maintenance ($200-$1,000), cybersecurity measures ($500-$2,000), and data storage ($100-$500).
Most shops report net annual profits increasing by 10-20% after implementing an all-encompassing software solution.
Streamlining Daily Operations Through Software Integration
Modern software solutions transform routine shop operations into streamlined, efficient processes. Through extensive integration, these systems connect various aspects of daily business activities, from administrative tasks to inventory management.
The software centralizes essential functions by combining scheduling, invoicing, and customer communications into a single dashboard. The system’s customer portal access provides clients with convenient self-service options for tracking repairs. Technicians can access real-time updates on work orders, while automated notifications keep customers informed about service progress. Digital work logs and integrated diagnostics reduce repair time and minimize errors.
Resource management becomes more precise with automated inventory tracking and supplier integration. Team collaboration improves through shared calendars, group chat features, and cloud-based access to critical information. This interconnected approach eliminates redundant tasks, speeds up workflow, and guarantees consistent service quality across all business operations.
Training Your Team and Maximizing Software Efficiency
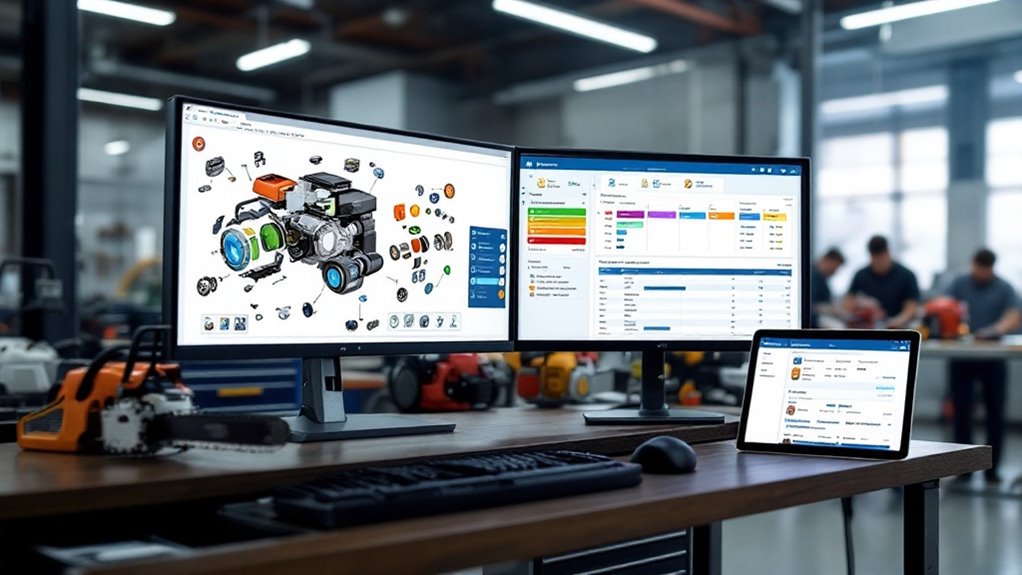
Successful implementation of small engine repair software depends heavily on extensive team training and optimization strategies. Through structured programs and consistent practice, businesses can guarantee their staff maximizes the software’s potential while streamlining daily operations.
Proper team training and strategic optimization form the foundation for successful software adoption in small engine repair operations.
Effective strategies include:
- Designate software champions within the team who receive advanced training and serve as go-to resources for troubleshooting and support.
- Implement modular learning approaches that break down complex software features into manageable segments, starting with core functions like invoicing and inventory.
- Utilize automated features for routine tasks such as payment reminders and service scheduling to reduce manual work.
- Monitor performance metrics regularly, tracking improvements in efficiency, error reduction, and customer satisfaction through built-in analytics tools.
For businesses working with advanced equipment like motorcycles, staff may need postsecondary training to effectively use software features related to computerized diagnostic systems.
Future-Proofing Your Repair Business With Technology
Staying competitive in the small engine repair industry requires businesses to embrace technological advancements and forward-thinking strategies. By implementing cloud-based diagnostic tools and IoT sensors, repair shops can monitor engines in real-time and identify potential issues before they become major problems.
Modern repair businesses are adapting by integrating extensive software solutions that streamline operations. These include automated scheduling systems, inventory management platforms, and CRM tools that enhance customer relationships. Additionally, shops are preparing for the future by investing in electric and hybrid engine repair capabilities. This transition is particularly important since EVs have 20-30% lower maintenance costs compared to traditional vehicles.
Sustainability plays a vital role in future-proofing operations. Smart shops are adopting energy-efficient tools, implementing recycling programs, and utilizing eco-friendly practices. Regular team training in emerging technologies and certifications helps to confirm that technicians stay current with industry developments, particularly in EV and hybrid repair techniques.
Frequently Asked Questions
Can Repair Software Integrate With Existing Diagnostic Tools and Equipment?
Modern repair software readily integrates with a wide range of diagnostic tools and equipment. These systems connect seamlessly with digital multimeters, scan tools, and specialized testing devices through various adapters and communication ports.
Integration enables real-time access to fault codes, testing procedures, and vehicle data across multiple platforms. Technicians can view diagnostic information instantly, perform automated tests, and access repair guidance directly through integrated software interfaces, considerably enhancing workflow efficiency.
How Secure Is Customer Payment and Personal Information in These Systems?
While some may worry about digital security, modern repair software systems employ robust protection measures. Customer data is safeguarded through industry-standard encryption protocols like TLS/SSL during transmission, and stored information is protected by secure firewalls and access controls. Most systems comply with PCI DSS standards for payment processing and include features like two-factor authentication.
Regular security audits, monitoring tools, and breach response plans further guarantee data safety and customer privacy.
What Happens to My Business Data if the Software Company Goes Bankrupt?
If a software company declares bankruptcy, business data faces several risks. The data could be sold as a company asset during liquidation, potentially exposing sensitive information. Security measures may weaken due to reduced staffing and oversight.
To protect business interests, companies should:
- Maintain independent data backups
- Include data protection clauses in contracts
- Have a backup software provider identified
- Document data recovery procedures
Early warning signs of financial instability should prompt immediate action to secure data.
Do These Software Solutions Work Offline During Internet Outages?
Perfectly prepared programs provide protection against problematic internet outages. Most modern business software solutions offer robust offline functionality, allowing operations to continue during connectivity disruptions.
While offline, users can typically access customer data, manage inventory, and generate invoices. Once internet connection resumes, the system automatically syncs any new data. However, some features like real-time payment processing may be limited during offline periods.
Can Customers Schedule Their Own Appointments Through the Software Platform?
Yes, customers can schedule their own appointments through the software platform’s self-service portal. The system allows 24/7 access via web or mobile devices, where customers can view real-time availability, select preferred time slots, and book services independently.
They can also include specific service requests, receive automatic confirmations, and manage their appointments through a password-protected account. This self-scheduling feature substantially reduces administrative work while providing convenient booking options for customers.
Conclusion
Statistics show that auto repair shops using management software see an average 25% increase in efficiency within the first year of implementation. For small engine repair businesses, embracing digital solutions is no longer optional but essential for survival and growth. By selecting the right software, providing proper training, and maintaining consistent usage, repair shops can substantially improve their operations, customer satisfaction, and bottom line in today’s technology-driven marketplace.